Feedback
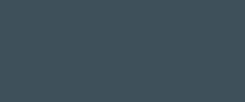
Steelmakers looking to get back on track
Steelmakers took a beating during the Great Recession. U.S. Steel, for instance, failed to turn a profit for five straight years.
But the path forward is clear.
Steelmakers have shaken up their leadership and cut costs, including by reducing staff and pulling the plug on suspect projects such as the effort to develop a coke substitute with Carbonyx at Gary Works. They have been working on structural changes that would allow them to profit even during downturns when the highly cyclical industry normally struggles.
In the future, local steelmakers hope to be more efficient, consistently profitable and competitive against a surge in imports that captured more than a quarter of the U.S. market share last year. They are also investing in technology, including developing high-strength grades that automakers can use to cut weight out of cars and meet new emissions standards that require twice the fuel efficiency by 2025.
Northwest Indiana’s two largest steelmakers – ArcelorMittal and U.S. Steel – have been moving in new directions. ArcelorMittal USA recently replaced longtime president and CEO Michael Rippey with Andy Harshaw to oversee the multinational company’s 27 facilities and 20,000 employees in the United States.
"We look forward to implementing and seeing the results of the October 2014 reorganization that involved the establishment of a North American flat-rolled segment to provide operational leadership and coordination to ArcelorMittal's North America operations," an ArcelorMittal spokesperson said.
"While we are committed to running our most cost-competitive assets at world-class production levels with no loss of overall volume or market share, we will continue to focus on increasing the efficiency of our facilities and the productivity of our workforce."
ArcelorMittal has been idling Indiana Harbor West's finishing operations in East Chicago, displacing hundreds of workers, and warned the union it planned to shut down the electric arc furnace in Indiana Harbor Long Carbon. The company is also looking to idle the No. 1 aluminizing line at the former LTV steel mill in December to shift the production to the new AM/NS Calvert plant in Alabama.
The Luxembourg-based steelmaker bought the steel processing plant as a joint venture with Nippon Steel & Sumitomo Metal Corp. The finishing facility, which can crank out 5.3 million tons of rolled steel a year, is closer to the newer automotive factories that have sprung up across the south. ArcelorMittal describes it as one of the most state-of-the-art in the world.
The company's global R&D Center in East Chicago also has been developing some of the most advanced grades of steel, which are stronger so less of it can be used in auto frames and other car parts.
"With continued innovation and hard work, ArcelorMittal is positioned as the leader in developing steel solutions to help automakers meet the demanding CAFE standards of 54.5 miles per gallon by 2025," a spokesperson said.
Over the next five years, orders for advanced high-strength steels are expected to rise to 35 percent from 20 percent. That's why more than 80 are under development.
"We've increased our product development activities to continue to provide innovative steel solutions, and we've re-doubled our efforts in the R&D labs," a spokesperson said.
"We also continue to get out the message – to the auto CEOs, to our partners, policymakers and regulators – that steel remains the dominant material used in vehicles because of its ability to provide superior cost and performance ... Over the next few years, we will further advance the way steel is used in autos ... that will push the limits in terms of strength and formability for automotive applications."
U.S. Steel is also investing in technology, but looking back at the tried and true. The Pittsburgh-based company announced plans to replace the blast furnace at Fairfield Works in Alabama with an electric arc furnace that would require a small workforce, fewer raw materials and less electricity, since it could be run during off-peak hours and shut off when demand dictates.
New CEO Mario Longhi has said the company likely would operate more electric arc furnaces, which can turn scrap metal into rebar and other construction materials. Analysts have suggested mini-mill furnaces could replace conventional blast furnaces at Gary Works, given their age and the cost to replace them.
U.S. Steel cut an estimated $435 million last year, including by laying off non-union managers at Northwest Indiana operations in Gary and Portage. The company closed a mill in Ontario, Canada, and idle tubular facilities in Ohio and Texas when oil plunged to less than $50 a barrel for the first time in years.
The steelmaker closed two more coke ovens at its Granite City plant in Illinois and temporarily idled East Chicago Tin, laying off 369 workers for the foreseeable future.
While showing he's willing to make tough, unpopular decisions, Longhi has repeatedly said U.S. Steel must earn its right to profitability.