Feedback
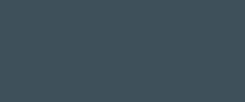
U.S. Steel Extends Its Transformation Amid a Challenging Market
Previously in this series, we discussed the Carnegie Way transformation of U.S. Steel (X). Through a disciplined approach, the company is working to strengthen its balance sheet with intense focus on cash flows, improving operational efficiency, optimizing supply chain, and right-sizing its operations.
Operational flexibility
There are two basic types of steel production processes: blast furnace (or BF) and electric arc furnace (or EAF). U.S. Steel produces all of its steel through blast furnaces. The chart above shows the steel production process in an EAF.
A blast furnace has high set-up costs compared to an EAF. As the fixed costs associated with BFs are higher, they severely affect the profits for steel companies in downturns. The reasoning is pretty simple. When production falls, fixed costs are divided among fewer units. This increases the per-unit production cost.
When capacity utilization rates are low, as they are currently, the profitability of steelmakers using blast furnaces comes down. On the other hand, steel companies using EAFs to produce steel generally don’t see huge swings in their profits.
Investment in EAF
U.S. Steel has announced an investment of $230 million to construct an EAF at its facility in Fairfield Works, Alabama. The construction will begin in 2Q 2015, and it’s expected to complete by 3Q 2016. EAFs will provide U.S. Steel with operational flexibility, as it’s much easier to adjust production levels in an EAF. Nucor (NUE) and Steel Dynamics (STLD) produce steel through EAFs. Currently, both form 3.7% of the SPDR S&P Metals and Mining ETF (XME). Carpenter Technology (CRS) forms 3.3% of XME.